The first crucial aspect in optimizing aircraft wing component fabrication processes is the utilization of advanced materials. These materials not only contribute to the structural integrity of the wing but also play a pivotal role in streamlining the fabrication process. Cutting-edge composites, alloys, and polymers are at the forefront, offering a perfect synergy of durability and weight efficiency.
Fabrication techniques have witnessed a revolutionary shift, incorporating automation and precision machinery. Suppose that a wing component on an aircraft is fabricated using automated processes such as Computer Numerical Control (CNC) machining and 3D printing. These technologies bring a new level of accuracy and repeatability, minimizing errors and optimizing the utilization of raw materials.
Another cornerstone in optimizing aircraft wing component fabrication processes lies in the implementation of smart manufacturing practices. The integration of Internet of Things (IoT) devices and sensors into the fabrication environment enables real-time monitoring and data analysis. This ensures that each step in the process is not only efficient but also adheres to the highest quality standards.
Suppose we delve into the realm of aerodynamics during the fabrication process. Computational Fluid Dynamics (CFD) simulations play a crucial role in refining the wing’s design for optimal performance. This iterative process, combined with real-world testing, allows for the creation of wings that are not only structurally sound but also contribute to fuel efficiency and aerodynamic excellence.
The human factor remains irreplaceable in the quest for perfection. Skillful technicians and engineers are the backbone of the aircraft wing component fabrication process. Continuous training programs and knowledge transfer mechanisms ensure that the workforce is adept at handling the latest technologies and evolving industry standards.
Optimizing aircraft wing component fabrication processes extends beyond the factory floor. The supply chain plays a critical role in ensuring a seamless flow of materials and components. Implementing just-in-time inventory systems and fostering collaborative relationships with suppliers contribute to the overall efficiency of the fabrication process.
Enhancing efficiency through computer aided design
Enhancing efficiency through computer-aided design (CAD) has revolutionized the way products are developed and brought to market. CAD software empowers designers and engineers to create, modify, and optimize designs with unprecedented precision and speed. The integration of CAD tools in various industries has become a cornerstone in achieving higher levels of productivity and innovation.
One of the key advantages of CAD is its ability to streamline the design process. By providing a digital platform for creating detailed 2D and 3D models, designers can visualize their concepts in a virtual environment, making it easier to identify potential flaws and make necessary adjustments. This not only reduces the time spent on manual drafting but also enhances the overall quality of the design.
Collaboration is another area where CAD excels. With the ability to share digital designs in real-time, teams located in different geographical locations can work together seamlessly. This collaborative approach fosters creativity and accelerates project timelines. Real-time collaboration features enable instant feedback and iteration, ensuring that the final design meets the highest standards.
Efficiency is further enhanced through the integration of parametric design capabilities in CAD software. This allows designers to create models with intelligent parameters, making it easy to modify and adapt designs as project requirements evolve. The parametric approach ensures that changes are automatically reflected throughout the entire design, eliminating the need for manual adjustments and reducing the likelihood of errors.
Automation is a game-changer in CAD, significantly boosting efficiency. Repetitive tasks can be automated, freeing up designers to focus on more complex and creative aspects of the project. This not only accelerates the design process but also minimizes the risk of human error. Automated simulations and analyses provide valuable insights, allowing designers to optimize their creations for performance, cost, and sustainability.
The impact of CAD is not limited to design alone; it extends to the entire product lifecycle. Integration with computer-aided engineering (CAE) and computer-aided manufacturing (CAM) systems ensures a seamless transition from design to production. This end-to-end approach minimizes the chances of discrepancies between the intended design and the final product, reducing waste and enhancing cost-effectiveness.
Implementing automated production techniques
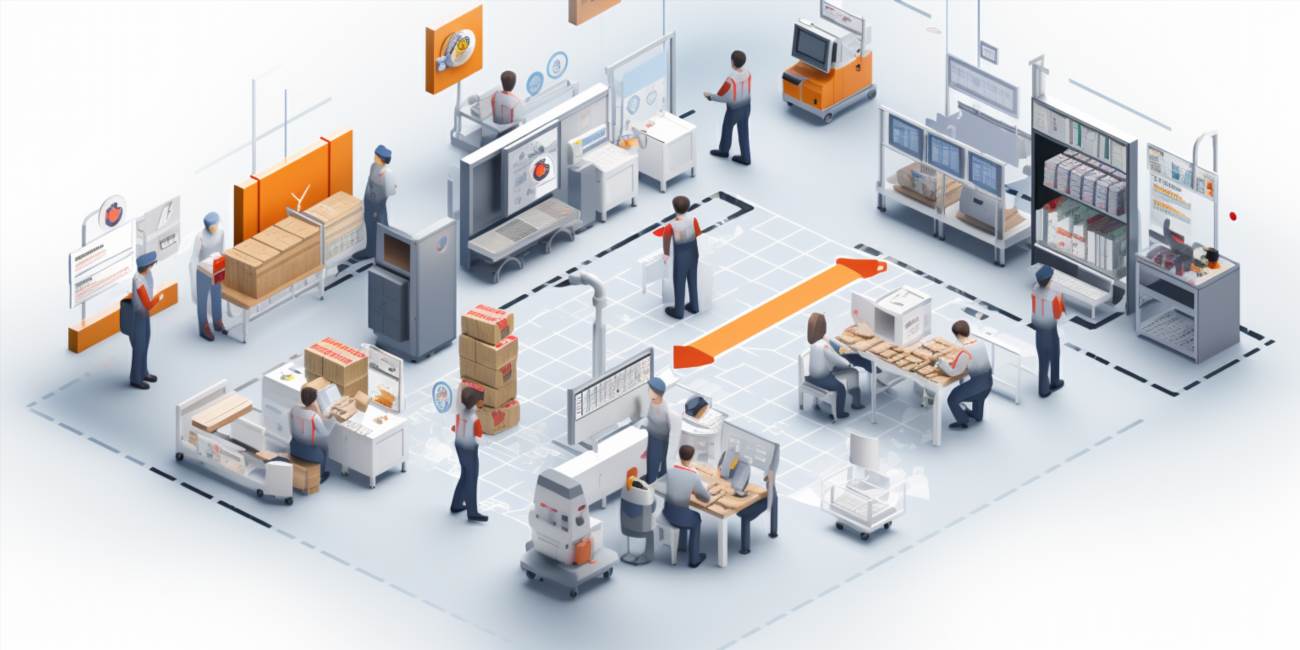
In the dynamic landscape of manufacturing, the integration of automation has become a cornerstone, reshaping traditional paradigms of production. The synergy between advanced technologies and intelligent robotics is revolutionizing how goods are manufactured, enhancing efficiency and precision.
The era of manual labor is gradually fading as automated production techniques take center stage. Manufacturing plants are now bustling with a new workforce – machines equipped with cutting-edge robotics. These robotic entities, programmed for intricate tasks, tirelessly contribute to the seamless flow of production processes.
One of the pivotal advantages of embracing automation in manufacturing is the remarkable increase in efficiency. Tasks that once consumed hours can now be executed with unprecedented speed and accuracy. The relentless nature of robotics ensures a consistent output, minimizing errors and optimizing the overall production cycle.
Automation also brings forth a paradigm shift in the skill set required in the manufacturing industry. While manual labor is progressively being replaced, the demand for skilled technicians to operate and maintain these robotic systems is on the rise. The marriage of human expertise with the precision of automation propels the industry forward.
Moreover, the integration of robotics in production processes enhances workplace safety. Hazardous tasks can be assigned to robotic counterparts, mitigating the risk to human workers. This not only ensures the well-being of the workforce but also reduces downtime caused by accidents, contributing to the overall efficiency of manufacturing operations.
The advent of automation and robotics does not only focus on speed and efficiency but also on resource optimization. Manufacturing plants implementing these technologies witness a reduction in waste, as precise control over processes minimizes unnecessary consumption of raw materials.
Integration, quality control, sensors
When it comes to software development, the process of integration plays a pivotal role in ensuring that individual components seamlessly come together to form a cohesive system. Integrating different modules involves the verification of their interoperability, making it a crucial step in the development lifecycle. It’s akin to assembling pieces of a puzzle, where each testing phase ensures that the integrated whole functions flawlessly.
In the realm of software engineering, quality control is the linchpin that safeguards the integrity of the final product. Rigorous validation processes are implemented to ascertain that the software meets specified requirements and adheres to predefined standards. This phase is akin to a meticulous examination, where every nook and cranny is scrutinized to validate that the software behaves as intended.
Sensors, the unsung heroes of technological advancements, are integral components in various systems. These electronic marvels enhance the capability of devices by collecting data from the environment. In the context of software, testing the sensor inputs becomes imperative to ensure accurate data acquisition. The verification of sensor data is a meticulous process, akin to calibrating instruments to guarantee precision.
Now, let’s delve into the intricate world of testing. Software testing is a comprehensive approach that involves executing the software to identify any discrepancies between expected and actual results. This crucial phase is not just about finding bugs; it’s about verifying that the software behaves according to specifications. Automated testing tools, a beacon in the realm of efficiency, assist in the verification process by systematically running test cases.
Verification, though crucial, is only one side of the coin. Validation, on the other hand, focuses on ensuring that the end product meets the user’s needs. It’s not merely about confirming that the software adheres to technical requirements but also about validating its utility in real-world scenarios. The intricate dance between verification and validation ensures that the software is not just technically sound but also practically beneficial.
In the grand scheme of software development, the interplay between integration, quality control, sensors, testing, and verification, validation forms a symphony of meticulous processes. Each note, represented by these keywords, contributes to the harmonious creation of reliable and efficient software solutions.